Training Flip Cards
The Why
We want to create the best possible structures for our Bar Managers, where there is space and time to focus on the mindset of 4-Wall Leadership. By moving focus away from weekly counts and day-to-day stock handling, we will give the Bar Manager an extended capacity to concentrate on daily tasks and leadership.
Introduction
Auto-count is a semi-automated count system that will help the Bar Manager, by giving more time to execute various tasks instead of counting the stock. The BM will be considered to have auto count for their store when they have mastered Stock handling and Type-in.
How Auto Count Works
Auto count is based on a mathematic formula, where three factors are used. Manual Count (MC), Buy In and Usage (POS Sale, Waste, Employee Meals) are used to calculate an Ultimo Stock (end stock).
Explain to the BM what each factor means:
Manual Count
The Manual Count is a regular count, except it is done monthly instead of weekly. The Manual Count is the foundation for the auto count formula to work, which is why it’s inevitable that the Manual Count is thoroughly done, to give a clear picture of the exact stock status.
Buy In
Buy in is all the goods that are delivered to the store including store transfers. This is determined by the store ideals.
Usage
The usage is calculated from all the POS Sales, Employee Meals and items wasted on the waste feature. To calculate the usage, it requires the store to have a good type-in culture, where all extra toppings, milks, employee meals are typed in on the POS. Furthermore, the stores must waste all items that are not used due to expiration, items lost on the floor, products not sold, etc.
Ultimo Stock
The Ultimo Stock is calculated from the Manual Count, Buy In and Usage. This is done by adding the Manual Count and the Buy In together, and then subtract it with the Usage, which results in the Ultimo Stock.
Explain the illustration below to give the BM a better understanding of the calculation.
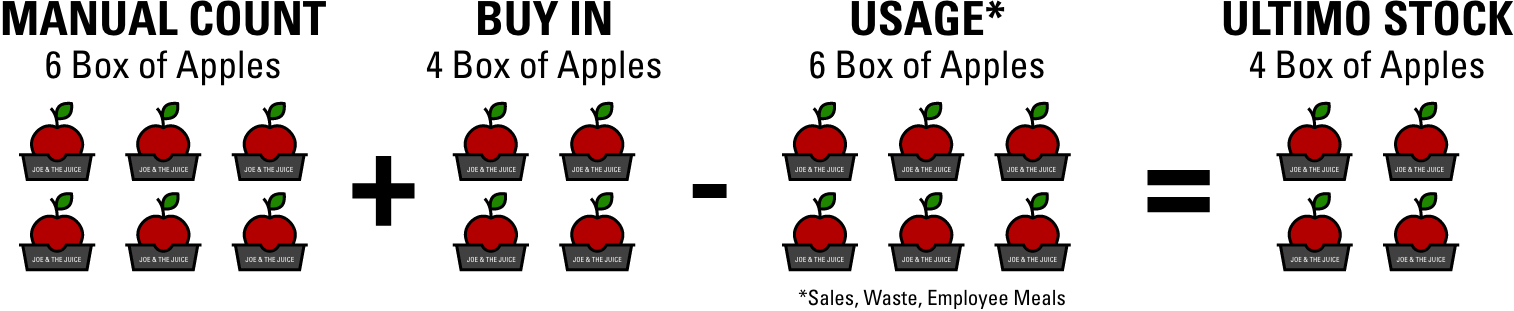
The Ultimo Stock is an almost accurate forecast, which is now used to calculate the needed Buy In for the next weeks. In order to assure a minimum of delivery mistakes, the BM needs to compare their stock to the Uploaded Count (further explanation later).
Go through the illustration below with the BM. Explain how the auto count works from EOM Count to the next EOM Count, and the weekly tasks that ensures an ideal stock holding.

Remember that the Manual Count 1 & 2 is important to count. These 2 counts will define the monthly waste.
Friday Procedures
Every Friday the BM will receive an PDF file with expected stock on Friday mornings before delivery. The PDF stock report is a list based on the stock level Friday morning before delivery, where 12 Key and low stock items are pointed out. It’s the Bar Managers responsibility to cross check the PDF stock report with the current stock. If the current stock doesn’t match, the BM MUST report the differences to the Purchasing Manager. It's important to notice that this is a quick checkup that should take no longer than 20 minutes.
To train the Friday Procedures the Trainer will note down 12 items that corresponds to the current stock, where the Trainer will add some fictional deviations. The Trainer will then set-up a count for the BM, where the BM will crosscheck the 12 items with the stock, where the BM should be able to quickly spot the deviations.
*These 12 Key items, will always be the same every week, these will never change compared to the Low Stock items there will variate each week.
A deviation in the PDF stock report vs. the Actual Stock, is not when 1 banana is missing. A deviation is when 2 or more boxes of apples are missing, in other words, the deviation should be noticeable right away.
If the BM spots all the deviations and finished the crosscheck within 20 minutes, the BM has passed the Friday Procedure.
Tell the BM to follow the 5 steps below, to secure a stable and healthy stock going forward:
1) Open the weekly stock PDF on Fridays
2) Crosscheck the stock from the night before with the weekly stock PDF - note down larger deviations
3) Send an e-mail to the local Purchasing Manager with all the deviations found
4) If no deviations are found, send a confirmation e-mail to the Purchasing Manager that everything looks good
5) Done!
Key understanding and Actions
When the Bar Manager understands the fundamentals of Auto-Count, the BM can move on to understanding the more advanced knowledge behind the mathematic formula, waste and stock ideals.
The Trainer will explain and show the BM the key understandings that will help through the weekly process of Auto-Count:
Employee Meals (usage): Every product consummated by the team should be typed in on the POS as an employee meal. Every time an employee product isn’t typed in, it will look like pure waste.
Actions: Make all your juicer are informed about the Type In culture. Make sure they understand the rules of extra toppings as well, one pr. each product.
IMS (usage): Whenever IMS (Ingredients, Measurement, Sequence) is not followed, the over usage will seem like pure waste. Therefore, IMS MUST be followed at all times!
Actions: Train the IMS with the team and inform about the reason why it is important to follow these guide lines.
Waste (usage): It is important to use the Waste feature (link up to) as this is the tool for the Purchasing Manager to track why a store might have a high waste percentage. It is very important to register waste so there is a clear picture of all goods leaving the store. This will affect the next delivery to be more precise.
Actions: Remember to follow up with the team at all times and explain why it is important to register waste each time.
Stock: Be observant over how the stock looks like on daily basis. It is important to have an overview over which ingredients is missing, low or overstocked.
Delivery (buy-in): Remember to follow up on the number of goods delivered to your store. Missing goods can appear as pure waste if not registered. Make sure to have registered the correct amount of goods “going in” the store, using Store Task. If some of the goods are in a bad condition after receiving the delivery. Contact your local Purchasing Manager and ask for a credit note for the current ingredients and follow the Purchasing Managers advise.
Actions: Follow up on all the received delivery to find all the low quality items and any other issues with the delivery and remember to contact/follow up with your local Purchasing Manager at all times.
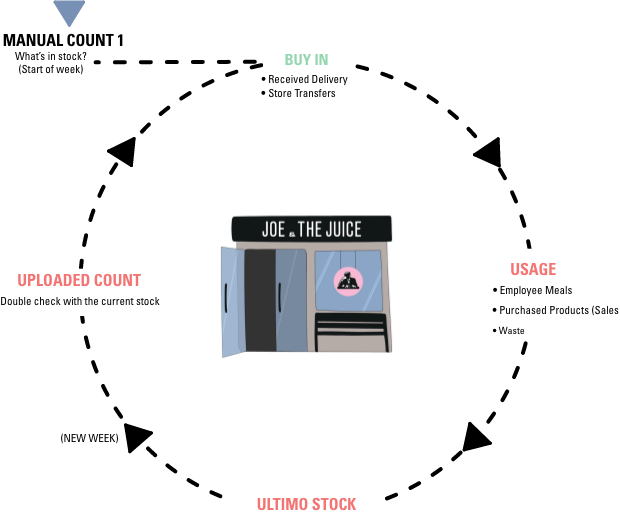
POS Type In: Make sure the team working BTC understand the importance of correct type-in on the POS.
Example of wrong type in on the POS:
One guest orders 3 Yellow Latte (corresponds to 1 litre/0.25 gallon of milk), the guest would like the three Yellows to be with Semi Skimmed Milk. When three Yellows are typed in, the POS will choose whole milk as the default milk, if this is not corrected the following scenario will happen.
Because the three Yellows are based on Semi Skimmed Milk there will be missing 1 litre/0.25 gallon of Semi Skimmed Milk in the Ultimo Stock whereas there will be an over stock of 1 litre/0.25 gallon of whole milk. If this is an ongoing issue, it will ultimately result in an overstock of Whole Milk and the store running Out of Stock on Semi Skimmed Milk. This is because the deliveries are based on the Ultimo Stock.
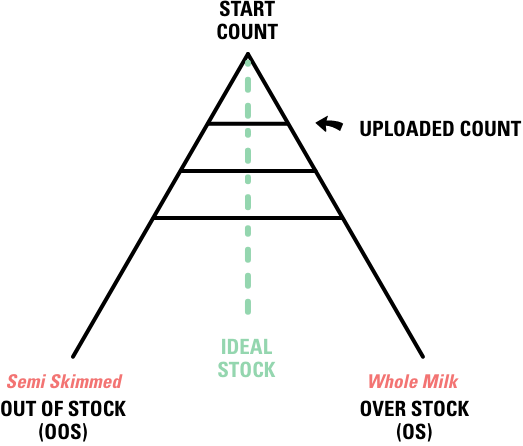
These five steps is some of the most frequent actions that will affect the Auto-Count in a bad way.
The Trainer will sum up together with the BM how to handle all five situations and how to change the situation in to a positive way.
Choose your bar type
‘Ingredients, Measurement, Sequence’. What is in the product, how much of each ingredient and in which order it is added to the product.
Point Of Sale – Is our customized “Point of Sale” system where we can handle payments from guests, employee meals and JOE Card redeeming. It is a system made to simplify the task of handling the different “point of sale” for us, while collecting the information for our database on our Workplanner.
A feature on The List to register everything we waste for whatever the reason might be. This is to make sure we account for everything in the bar and minimize the ‘Grey Area’ of unaccounted waste.
Refers to being both time and waste efficient by switching between the spill cup blender and other blenders. This is performed by pouring excess apple juice into the blender before proceeding with making the juice.
First in first out – FIFO is fundamental for a healthy stock handling. FIFO means “First In, First Out”. FIFO is the goods “workflow” from when we receive our goods, to which order we use them. It is important to make sure you stack up the oldest food items on top / in front.
Regional Manager – The extension of the country management. BTC Mentor for all stores and head of communication between respective stores.
Bar Manager – The most important position in JOE & THE JUICE! Combines Operational Management Expertise and 4-WALL LEADERSHIP to optimize 4-WALL OPERATIONAL PERFORMANCE. Leads own store and team with Clear Optics. Develops the foundations to lead your team and store to OPERATIONAL PERFORMANCE. Also provides constructive feedback to RM in relation to the store and team performance